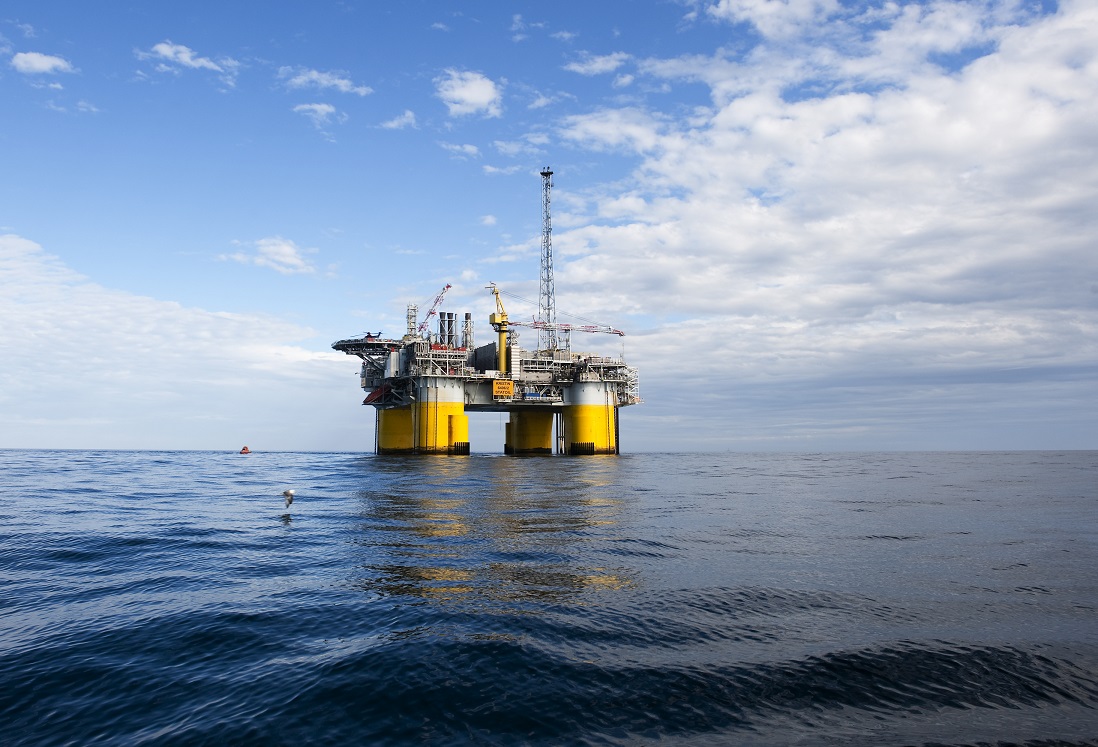
Kristin.
Nøyaktig kontroll
Hvert sjette år blir gassbehandlingsanlegget ved Kårstø stengt for å utføre en stor overhaling av alle fasilitetene. Det krever planlegging, ekspertise og nøyaktighet for at alt skal gå etter planen, og ha en god flyt. Kårstø benyttes til en betydelig del av Norges gasseksport, enhver forsinkelse kan bli svært kostbar.
Kårstø, som ligger nord for Stavanger, er stedet hvor Europas største gassbehandlingsanlegg befinner seg. Anlegget spiller en viktig rolle i transport og behandling av gass og kondensat. 32 felt fra hovedområder på den norske kysten leverer daglig til Kårstø via tre rørledninger. Den behandlede naturlige gassen og kondesatet blir så levert til Europa via to rørledninger. 25 prosent av Norges årlige gasseksport til Europa går via Kårstø. Kårstø kan motta 93,7 Sm3 med naturlig gass. I tillegg mottar det kondensat og lettolje fra sin egen rørledning. Kårstøanlegget, inkludert gassrørledningene til og fra anlegget, eies av Gassled og drives av Gassco, mens Statoil er ansvarlig for teknisk drift og har utviklet størstedelen av gassinfrastrukturen.
Sikkerheten først
På anlegget fokuseres det fullt og helt på sikkerheten. I tillegg til strenge sikkerhetsrutiner for de 750 ansatte og 400 leverandørene, finnes det også 2 300 gassdetektorer, 750 flammedetektorer og 100 kameramaster. Anlegget må også kontrolleres regelmessig. Hvert sjette år utfører Statoil en kontroll som gir full vurdering av vedlikeholdet ved anlegget. «Du kan sammenligne det med et fly. Etter en flytur går vedlikeholdsansvarlige gjennom flyet og utfører nødvendig vedlikehold, slik at flyet er sikkert og klart før det letter igjen», sier Karl Børge Ask, driftsingeniør hos Statoil. «Det finnes selvsagt også økonomiske grunner til at vi må ha et system som fungerer feilfritt, men hovedfokus er sikkerheten.»
Krever nøye planlegging
Planlegging av kontroll begynner allerede mellom ett og et halvt og to år i forveien. «Generelt sett bruker vi like mange timer på planlegging som vi gjør på å utføre kontroll og vedlikehold», sier Ask. «Det er som et stort puslespill som må legges på plass, hvor logistikken er veldig viktig», sier Ask. «Omtrent 86–90 tusen timer går til å utføre kontrollen, mens omtrent 86 tusen timer går til alle forberedelsene. Det betyr at halvparten av tiden går til planleggingen. Men det er veldig viktig.» Samtidig som at det er viktig å få jobben gjort uten feil, må man også tenke på innkvartering og mat til de ekstra ansatte.
For kontrollen alene, hadde Statoil 10 store kontrakter med leverandører og 30 underleverandører. Midlertidig innkvartering for over 400 mennesker og mattelt ble satt opp inne på området. 1 000 mennesker jobbet på anlegget under kontrollen. Alle som jobber under kontrollen må ta et sikkerhetskurs, mens de som jobber mer enn 14 dager ved anlegget også må ha en hel dag med sikkerhetsopplæring.
Det er avgjørende å ha et helt gassfritt anlegg
I perioden 27. august til 15. september ble Kårstøanlegget stengt for overhaling og vedlikehold. 10 av disse dagene ble brukt til vedlikeholdsarbeid. Det er ekstremt viktig at alle gassrørledningene i behandlingsanlegget er helt fritt for hydrokarboner før vedlikeholdsarbeidet kan begynne. Rørledningene må tømmes for oksygen før de fylles opp igjen med gass fra feltene. Fire dager før og fire dager etter vedlikeholdsarbeidet ble utført var rørledningene tomme for gass. AGA leverte omtrent 1 200 tonn med flytende nitrogen som ble brukt til å tømme gassrørledningene før og etter vedlikeholdsarbeidet.
«I tillegg til den stasjonære hovedtanken på 200 m3, satte vi opp fire ekstra nitrogentanker på 4 cc og 10 ekstra dumpere på forskjellige steder utenfor behandlingsanlegget, slik at vi kunne levere nok nitrogen til Statoil», sier Kjetil Veidel, applikasjonsingeniør og øverste kontoadministrator ved Statoil. «Statoil produserer selv nitrogen, men ikke nok, så vi hadde to kjøretøy om dagen som leverte nitrogen under kontrollen», fortsetter Veidel. «Statoil stoler fullt ut på AGA og har gitt oss fri tilgang. For eksempel har vi tilleggslisenser for sjåførene. Vi tar oss av alle leveringer og det administrative arbeidet som følger med disse selv.»
«Vi har de prosedyrene og rutinene som kreves for slike prosjekter. Produksjons- og logistikkavdelingene våre er veldig dyktige når det gjelder planlegging av slikt arbeid, og vi har en stor fordel med høy produksjonskapasitet fra mange omfattende luftseparasjonsanlegg på strategiske plasseringer rundt om i regionen. AGA-teknikerne våre har også mye erfaring med denne typen prosjekter og er ofte tilgjengelige døgnet rundt. De kan komme inn om nødvendig for å sikre at kunden alltid mottar den gassmengden som de trenger. Vi har også teknisk support som kan handle raskt når det er nødvendig», sier Veidel. «Det neste prosjektet vil være kontroll av anlegget på Melkøya i 2017. Det vil kreve to års planlegging, inkludert logistikk og utstyr», legger han til.
Raskt og feilfritt med spesialkompetanse
«Siden vi ikke har råd til forsinkelser, er det ikke bare planlegging som er viktig. Vi må også vite at vi kan stole på alle leverandørene som vi samarbeider med. Vi vil ha de beste, selv når det gjelder ting som leverandør av ventiler», legger Ask til. «For eksempel, har vi leid et team med klatreeksperter og et spesialistteam fra Molde som skal bytte ut de tre gassfaklene. Systemet må være helt tomt når gassfaklene tømmes, siden de brenner dem ut», sier Ask. Gassfaklene byttes ut ved hjelp av helikoptre. Det tar omtrent en halvtime å bytte ut én gassfakkel.
«AGA er en viktig del av puslespillet under kontrollen, for uten nitrogen til å tømme gassrørledningene ville arbeidet ha stoppet opp. Så det er veldig viktig at leveringen kommer når den skal», fortsetter Ask. «AGA har hatt full kontroll hele tiden, og vi har aldri hatt en grunn til å bekymre oss eller føle at vi må blande oss inn. Det at AGA har tidligere erfaring med denne typen arbeid er en stor fordel. Verdier på mer enn 200 millioner passerer gjennom anlegget hver dag, så vi snakker om gigantiske tap for Norge hvis det oppstår forsinkelser», oppsummerer Ask.
Linde vant byggekontrakten og en tysk skoleklasse
Linde Engineering vant kontrakten for design og konstruksjon av den første bygningen i Kårstø, som ble satt i drift i 1985. Flere ingeniører fra Linde flyttet til Norge for å være til stede i årene under konstruksjonen. Siden mange tok med seg familiene sine til Norge ble det opprettet en skreddersydd skoleklasse for barna. Størstedelen av undervisningen foregikk på tysk og fulgte tysk pensum, for å gjøre det enklere for barna å vende seg til det tyske samfunnet igjen når familiene flyttet tilbake. På det meste gikk det tjue barn av de tyske ingeniørene på den norske skolen.