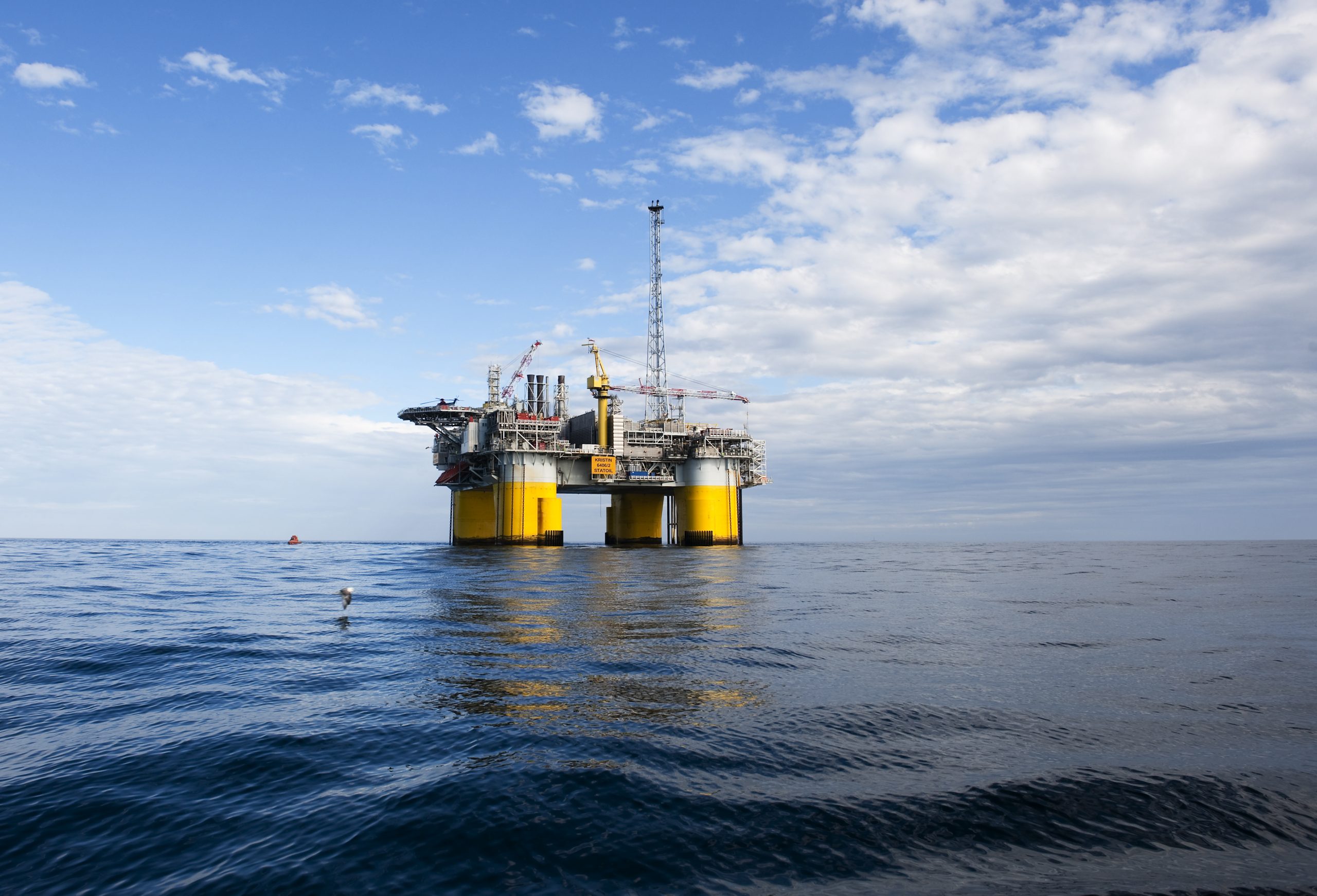
Precise auditing – maintainance stop at Kårstö
Every six years, the gas processing plant at Kårstö is shut down for a major overhaul of the entire facility. It requires planning, expertise and accuracy to keep it on schedule and get everything to flow according to plan. Kårstö accounts for a significant part of Norway’s gas exports, and therefore any delay could be very costly.
Kårstö, north of Stavanger, is the location for Europe’s largest gas processing plant. The plant plays a crucial part in the transportation and processing of gas and condensate. Thirty-two fields from key areas on the Norwegian continental shelf deliver daily to Kårstö via three pipelines. The processed natural gas and condensate are then delivered to Europe via two pipelines. Twenty-five percent of Norway’s annual natural gas exports to Europe go through Kårstö. Kårstö is able to receive 93.7 Sm3 of natural gas. In addition, it receives condensate and light oil from its own pipeline. The Kårstö plant, including the gas pipelines to and from the plant, is owned by Gassled, and operated by Gassco, while Statoil is responsible for the technical operation and has developed the largest part of the gas infrastructure.
Safety first
At the gas processing plant, there is a total focus on safety. In addition to rigorous safety routines for the 750 employees and 400 suppliers, there are also 2,300 gas detectors, 750 flame detectors and 100 camera masts. The plant must also be reviewed periodically. Every sixth year, Statoil carries out an audit, a complete review of the maintenance of the facility. “You can compare it with an aircraft. After a flight, maintenance staff goes through the aircraft and does the necessary maintenance, so the plane is safe and sound before the next take off,”, says Karl Börje Ask, operations engineer at Statoil. “There are, of course, also economic reasons for having a system that works flawlessly, but the major reason is safety.”
Requires careful planning
The planning of an audit begins between one and a half and two years in advance. “In general, we spend the same number of hours on planning as we do on the actual audit and maintenance work,” says Ask. “It’s like a giant jigsaw puzzle to be put together, in which logistics play a major part,” says Ask. “Roughly 86-90 thousand hours are spent on the audit work and about 86 thousand hours go into the preparations, so half the time goes to planning. But it is really important.” Besides the importance of getting the job done without any mishaps, the accommodation and food supply for the extra staff also require planning.
For the audit alone, Statoil had 10 main contracts with suppliers and 30 subcontractors. Temporary accommodation for over 400 people and food tents were set up inside the area. During the audit some 1,000 people worked at the plant. Everyone who works on an audit must pass a safety course, while those who work more than 14 days at the plant need a full day of safety training.
It´s crucial to have a completely gas-free plant
During the period between 27 August and 15 September, the Kårstö plant was shut down for overhaul and maintenance. Of the entire audit period, 10 days were allocated to maintenance work. It is extremely important that all the gas pipelines in the processing plant are completely free from hydrocarbons before the maintenance work begins, and the pipelines need to be emptied of oxygen before they are refilled with gas from the fields. Four days before and four days after the maintenance work, the pipelines are emptied of gas. AGA delivered about 1,200 tons of liquid nitrogen for draining the gas pipelines before and after the maintenance work.
“In addition to the stationary main tank of 200 m3, we set up four extra 40cc nitrogen tanks and 10 extra dumpers in various places outside the processing plant to be able to provide Statoil with nitrogen,”, says Kjetil Veidel, Application Engineer and Key Account Manager for Statoil. “Statoil produces nitrogen itself, but not enough, so we had two cars a day supplying nitrogen during the audit,” continues Veidel. “Statoil have great confidence in AGA and they have given us free access. For example, we have accompanying license for the drivers and we take care of all the deliveries and administrative work related to the deliveries ourselves.”
Linde Engineering won the contract for the design and construction of the first building at Kårstö, which began operating in 1985. Several engineers from Linde moved to Norway to be in place during the years of the construction. As many brought their families with them to Norway, a tailor-made school class was arranged for the children. To make it easier for the children to acclimatise themselves once they moved back to Germany, a significant part of the teaching was done in German in accordance with the German curriculum. At most, about twenty of the German engineers´ children were enrolled in the Norwegian school.
“We have the procedures and routines for this kind of project. Our production and logistics departments are very skilled at planning work of this kind, and our major advantage is our large production capacity from our many large-scale air separation plants in strategic locations in the region. Our AGA technicians also have great experience of this type of project and often work 24/7 or can be called in quickly to ensure that the customer always receives the required gas delivery. Our technical support is also present and can act quickly if required,” says Veidel. “The next project will be the audit of the plant at Melköya in 2017. It requires a two-year planning process including logistics and equipment,” he adds.
Fast and smooth with specialist competence
“Since we cannot have any delays, planning is not the only important thing. We need to know that we can rely on all the suppliers we work with. We want the best even if when comes to the valve suppliers,” adds Ask. “For example, we have hired a team of climbing experts and a specialist team from Molde for the replacement of the three gas flares. The system must be completely empty when the gas flares are emptied since they burn them out,” says Ask. The gas flares are replaced using helicopters. It takes about half an hour to change a gas flare.
“AGA is an important piece in the audit puzzle, because without the nitrogen to empty the gas pipelines the work would stop. So supply accuracy is very important,” continues Ask. “AGA has been in full control at all times and we have never had any reason to worry or to feel the need to interfere. The fact that AGA has previous experience of this kind of work is a major advantage. Values of more than 200 million (approximately 22 M €) pass through the plant each day, so we’re talking about huge losses for Norway in case of any delay,” summarises Ask.
By: Cecilia Rudengren,
Photo: Statoil