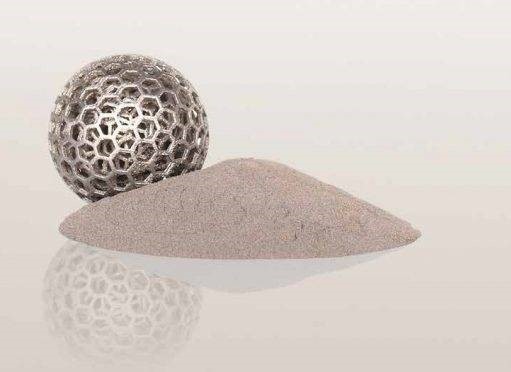
Beyond the boundaries in high temperature component design
Great minds think alike, it’s been said, and the recent collaborative project between Linde Region Europe North and Kanthal (part of Sandvik Group) demonstrates this truth. Thinking outside the box and finding new geometries are some of the results of their joint move into additive manufacturing with heat resistant material.
Linde Region Europe North (former AGA), founded some 115 years ago, is an old-timer in Swedish industrial history as well as a persistent pioneer.
“We have been looking into the possibilities of additive manufacturing over the last couple of years,” says David Muren, Rebox team manager at Linde Region Europe North. “I’ve seen it as a great way of shortening the prototype route.”
This interest coincided with Kanthal’s additive manufacturing development, and when Miles Cao, technical specialist in additive manufacturing and powder at Kanthal, mentioned the possibility of a cooperation, Muren was interested in focusing on one specific component as a joint project.
“It’s a replacement for an existing burner nozzle to create a different flat flame,” Muren says. “That’s something we’ve been looking at using traditional manufacturing methods, but additive manufacturing is a quicker way to achieve it. We had actually already discussed the design work, so when Cao asked us to supply them with the first outline of the design, that’s what we did.”
To produce the burner nozzle, Linde had earlier used traditional subtractive manufacturing methods, such as lathing and grinding.
“The traditional method has limitations when it comes to the inside of the nozzles,” Muren explains. “Inside is where most of the activity is going on, when it comes to the gas streams passing through. However, it’s really hard with the older methods to reach inside the small intrinsic nozzles, which are only 12 to 15 millimeters in diameter.”
With additive manufacturing technology there are no limits in either design or reach. Cao explains that Kanthal offers the most common method of additive manufacturing known as selective laser melting.
“It’s a powder-based technology where you melt layers of layers of powder using a laser,” he says. “Now you can create features such as internal channels and complex geometries, which is only possible with 3D printing, or would at least be very difficult with traditional manufacturing.”
Using a material suited for high temperature processes in additive manufacturing is a revolutionary innovation.
“Iron-chromium-aluminum provides unique performances for our customers. The material offers high-temperature corrosion and oxidation resistance,” says Cao. “It has superior high temperature strength, especially in temperatures above 1000 degrees Celsius. We can now utilize iron-chromium-aluminum alloys in additive manufacturing to create new products.”
Among the benefits of additive manufacturing, Muren cites the short prototyping process period as well as the intrinsic design that lets the burner “breathe.” He adds that the manufacturing project has resulted in a nozzle with better flow, which is much more “gas dynamic.”
Using a powder-based additive manufacturing technology means that Linde can move away from bars as raw material, traditionally used in subtractive manufacturing. With additive manufacturing almost any geometry can be achieved through smart design, sent to the 3D-printer and then pressing start. But such change doesn’t happen overnight.
“The main challenge has been to think completely differently from how a traditional designer thinks, to lose the boundaries based on traditional methods,” Muren says. “Additive manufacturing has other boundaries, but we haven’t really figured those out yet.”
The two companies are thinking alike, and Linde is now peeking outside the box.
“I think the traditional way of manufacturing is still good, and we’ve done great stuff over the years,” Muren says. “But additive manufacturing will add to it, and I personally think that a combination of traditional and additive manufacturing where it’s needed is the strongest and most promising way forward. We have definitely gotten our feet wet.”
Text and video: Kanthal, part of Sandvik Group, https://www.kanthal.com/