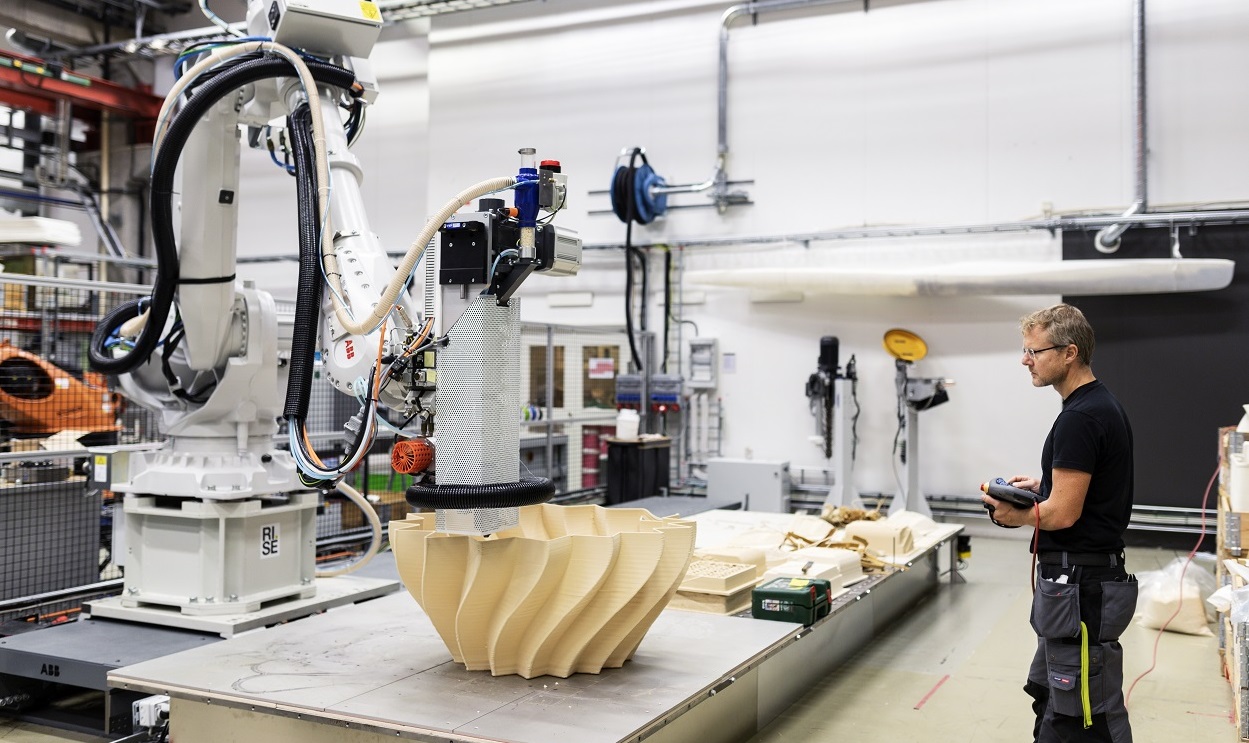
Additive Manufacturing: a high-tech RISE to the top
A revolutionary 3D-printing technology is helping propel a unique Swedish research consortium toward the leading edge of additive manufacturing.
“Additive manufacturing allows us to push the boundaries for how various parts can be made,” says Seyed Hosseini, who is Head of the Additive Manufacturing team at RISE as well as a researcher at Chalmers University of Technology in Gothenburg.
“It allows us to manufacture parts in ways that were impossible before.”
Founded a decade ago, RISE came into being as part of a government effort to reorganize and rejuvenate Sweden’s research sector that started back in the 1990s. Today, the independent, state-owned research institute has 2,800 employees housed at various labs and universities around the country and an annual turnover of more than 3 billion SEK. Industrial partners account for about half of RISE’s revenues, with the remainder coming via government grants and other public funding bodies such as universities.
Pioneering research
Hosseini’s team is one of several research groups at RISE carrying out pioneering research in areas ranging from energy to health to mobility. They focus on additive manufacturing, which relies on equipment powered by computer-aided design (CAD) or 3D-scanners. These “printers” can use a variety of materials – metal powder, polymers, glass – to build three-dimensional objects one layer at a time. While Hosseini can’t divulge exactly what sort of parts he and his colleagues at RISE are printing, he reveals they are working with metallic materials, polymers as well as ceramics.
While all additive manufacturing processes require a high degree of precision, 3D-printing with metallic materials poses a particular challenge, requiring careful monitoring throughout the printing process to ensure the quality of the final product.
“The atmosphere in the printing chamber plays an important role because if you have high oxygen content during the print, it could lead to formation of unwanted internal defects”
“The atmosphere in the printing chamber plays an important role because if you have high oxygen content during the print, it could lead to formation of unwanted internal defects,” Hosseini explains. While some alloys used in 3D-printing are more sensitive to oxidation than others, they all require careful monitoring and control in order to understand the process and ensure the quality of the printed parts.
An emerging technology from Linde
Indeed, the team’s early efforts 3D-printing with metallic materials didn’t produce the desired results. To help identify what wasn’t working, Hosseini and his team were able to test an emerging technology from Linde Gas in early 2017 that could accurately measure and control the oxygen levels in 3D-printing chambers.
Known as ADDvance™ O2 precision, the technology continuously analyses the printer chamber’s atmosphere. It has the power to detect oxygen concentrations as low as 10ppm and automatically adjust the gas mixture in the chamber accordingly.
“The system provides a real-time picture of oxygen levels in the chamber so you can follow the values over time,” explains Bo Williamsson, the Additive Manufacturing Applications Manager at Linde Gas, region Europe North.
Williamsson and his colleagues played an integral role in the installation of ADDvance at RISE, which also allows researchers to maintain oxygen levels in the printing chamber to a specific level.
“It’s sort of like a cruise control for gases in the chamber. The level remains constant throughout the printing process,” he explains.
Optimizing alloys
The technology helps the Additive Manufacturing team at RISE optimize the atmosphere in their printer chamber and better understand what adjustments needed to be made, as well as what effects it has on the printed product. The data gathered while monitoring the printing process also contributes to a certification process that connects each printed product with a detailed record of its production.
Since most alloys used in 3D printing today weren’t specifically designed for additive manufacturing, the insights from the ADDvance™ system help create an opportunity for the team to further optimize the alloys and take advantage of the inherent properties of the process.
“We’re seeing a lot of interesting results right now. Since we can now monitor the process much more closely, we’re also able to better understand why the material behaves the way it does,” Hosseini explains.
“A powerful tool”
He credits the team and equipment from Linde with playing an important role in advancing his researchers’ understanding of 3D-printing using metals that are susceptible to oxidation.
“The ADDvance™ system is a powerful tool that provides the level of detail we need to help us better understand the entire 3D-printing process,” he says. “We’re also getting more insights and more accurate insights for how to improve the process.”
Linde continues to service the equipment and supply the necessary gases to operate the ADDvance system. The collaboration has also resulted in an extensive knowledge exchange between the additive manufacturing teams at RISE and Linde Gas as Hosseini and his team continue to work toward wider implementation and industrialization of additive manufacturing techniques.
“Additive manufacturing will have an impact across many sectors, but exactly how depends on the specific sector,” he explains.
In aerospace, for example, additive manufacturing can help create more high-strength, lightweight materials resulting in lighter, more fuel-efficient aircraft.
Creating “digital twins”
In the energy sector, 3D-printing with metals can also help produce new parts that improve the efficiency of heat exchangers and gas turbines, lowering emissions, and their overall carbon footprint. According to Hosseini, a few global companies are already using 3D-printing techniques in this way to make a difference.
Looking ahead, he expects many exciting developments in the coming years, in particular when it comes to streamlining the supply chain and implementing a more robust digital eco-system around additive manufacturing. Here too the ADDvance system has an important role to play by increasing connectivity, facilitating “on-line” quality assurance and data management, as well making it easier to create “digital twins” of objects before they are printed.
“Additive manufacturing is only one part of the eco-system,” he explains. “One of our tasks will be to connect the different parts of the supply chain, both physically and digitally.”